Pintakäsittelyn valinta on ongelma, jota jokainen suunnittelija kohtaa. Pintakäsittelyvaihtoehtoja on saatavana monen tyyppisiä, ja korkean tason suunnittelijan ei tulisi vain harkita suunnittelun taloutta ja käytännöllisyyttä, vaan myös kiinnittää huomiota kokoonpanoprosessiin ja jopa ympäristövaatimuksiin. Alla on lyhyt johdanto joihinkin yleisesti käytettyihin pinnoitteisiin kiinnittimiin yllä olevien periaatteiden perusteella kiinnittimen ammattilaisten viittaamiseksi.
Kello 1. Sähkökalvanisointi
Sinkki on yleisimmin käytetty pinnoite kaupallisiin kiinnikkeisiin. Hinta on suhteellisen halpa ja ulkonäkö on hyvä. Yleisiä värejä ovat musta ja sotilaallinen vihreä. Sen korroosion vastainen suorituskyky on kuitenkin keskimäärin, ja sen korroosionesto on alhaisin sinkkipinnoitus (päällystys). Yleensä galvanoidun teräksen neutraali suolahuihkeetesti suoritetaan 72 tunnin sisällä, ja myös erityisiä tiivistysaineita käytetään varmistamaan, että neutraali suolahumpailutesti kestää yli 200 tuntia. Hinta on kuitenkin kallis, mikä on 5-8-kertainen tavallisen galvanoidun teräksen hinta.
Sähkögalvanointiprosessi on alttiita vedynhallintalle, joten luokan 10.9 yläpuolella olevia pultteja ei yleensä käsitellä galvanoimalla. Vaikka vety voidaan poistaa käyttämällä uunia pinnoituksen jälkeen, passivointikalvo vaurioituu yli 60 ℃: n lämpötiloissa, joten vedyn poisto on suoritettava sähkösopulaation jälkeen ja ennen passiivista. Tällä on huono käyttökelpoisuus ja korkeat käsittelykustannukset. Todellisuudessa yleiset tuotantolaitokset eivät poista aktiivisesti vetyä, ellei tietyistä asiakkaista valtuutta.
Salvanoitujen kiinnittimien vääntömomentin ja ennalta kiristyvän voiman välinen johdonmukaisuus on huono ja epävakaa, eikä niitä yleensä käytetä tärkeiden osien kytkemiseen. Vääntömomentin esikuormituksen johdonmukaisuuden parantamiseksi voiteluaineiden päällystysmenetelmää pinnoituksen jälkeen voidaan käyttää myös vääntömomentin esikuorman johdonmukaisuuden parantamiseksi.
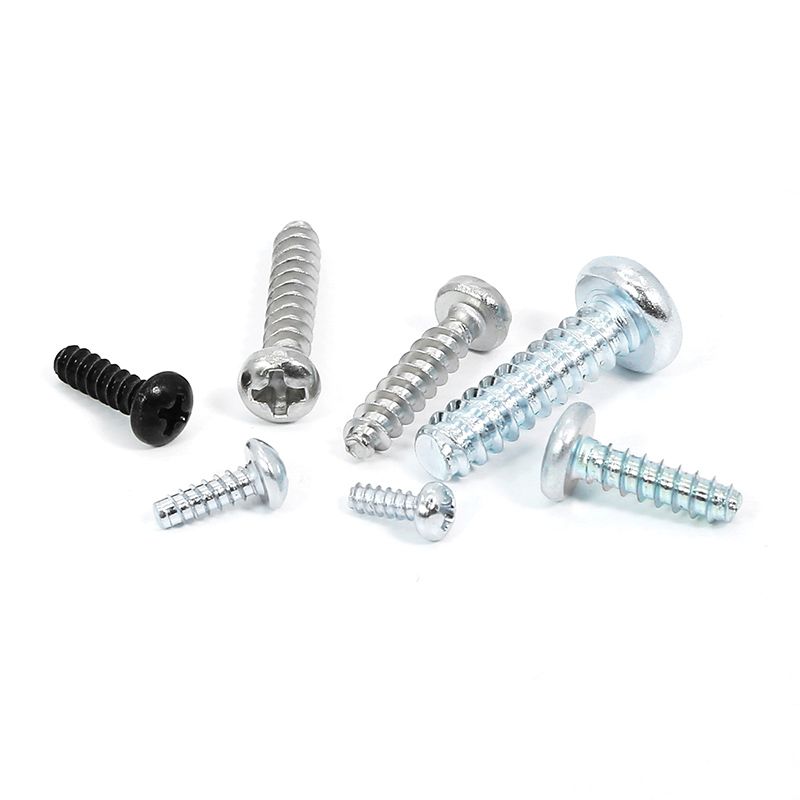
2. fosfatointi
Perusperiaatteena on, että fosfatointi on suhteellisen halvempaa kuin galvanisointi, mutta sen korroosionkestävyys on huonompi kuin galvanointi. Fosfatoinnin jälkeen öljyä tulisi levittää, ja sen korroosionkestävyys liittyy läheisesti levitetyn öljyn suorituskykyyn. Esimerkiksi fosfatoinnin jälkeen yleisen ruosteöljyn levittäminen ja neutraalin suolakäyttökokeen suorittaminen vain 10-20 tuntia. Korkealaatuisen ruosteöljyn levittäminen voi kestää jopa 72-96 tuntia. Mutta sen hinta on 2-3-kertainen yleisen fosfatointiöljyn hinta.
Kiinnittimiin on kaksi yleisesti käytettyä fosfatointityyppiä, sinkkipohjaista fosfaatiota ja mangaanipohjaista fosfaatiota. Sinkkipohjaisella fosfatoinnilla on parempi voitelun suorituskyky kuin mangaanipohjaisella fosfatoinnilla, ja mangaanipohjaisella fosfatoinnilla on parempi korroosionkestävyys ja kulutusvastus kuin sinkin pinnoitus. Sitä voidaan käyttää lämpötiloissa, jotka vaihtelevat välillä 225-400 astetta Fahrenheit (107-204 ℃). Etenkin joidenkin tärkeiden komponenttien kytkemiseksi. Kuten moottorin kytkentävarsipultit ja mutterit, sylinterin pää, päälaakeri, vauhtipyöräpultit, pyöräpultit ja mutterit jne.
Korkean lujuuden pultit käyttävät fosfrointia, mikä voi myös välttää vedynhallintakysymyksiä. Siksi teollisuuskentän 10.9 yläpuolella olevia pultteja käyttävät yleensä fosfatiivista pintakäsittelyä.
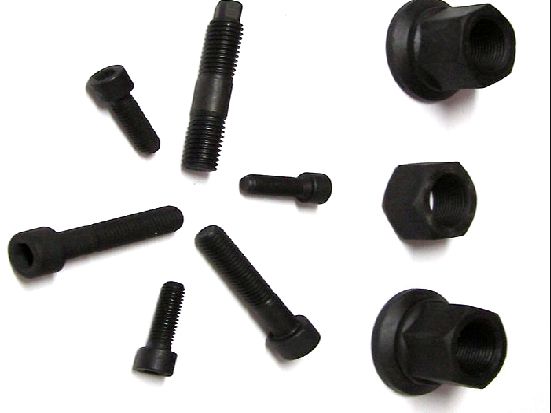
3. Hapettuminen (mustan)
Mustaminen+öljyt ovat suosittu pinnoite teollisuuskiinnikkeille, koska se on halvin ja näyttää hyvältä ennen polttoaineen kulutusta. Mukautuksensa vuoksi sillä ei ole melkein ruosteen ehkäisykykyä, joten se ruostuu nopeasti ilman öljyä. Jopa öljyn läsnä ollessa suola-suihkutesti voi kestää vain 3-5 tuntia.
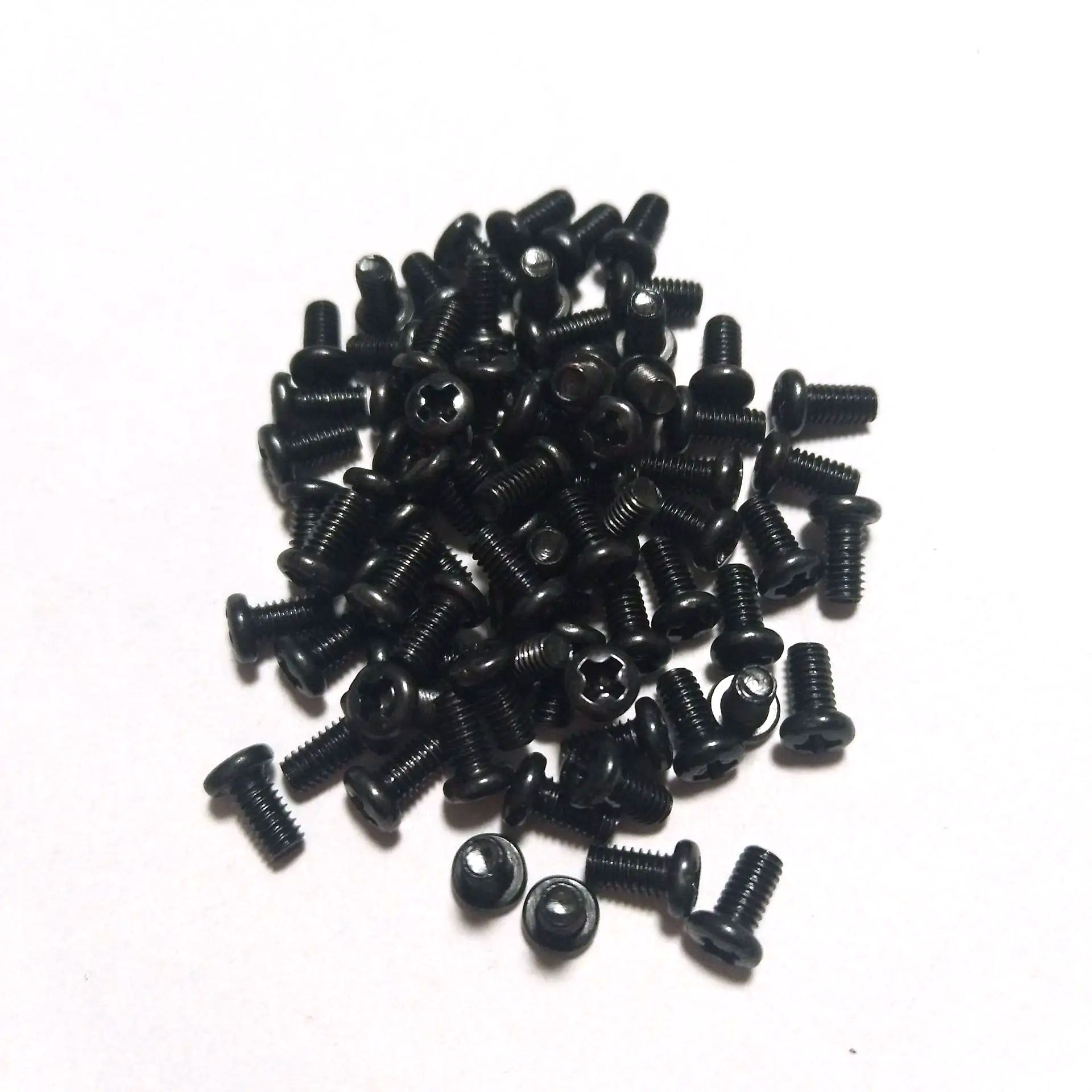
4
Kadmiumpinnoittelulla on erinomainen korroosionkestävyys, etenkin meren ilmakehän ympäristöissä, verrattuna muihin pintakäsittelyihin. Jätteiden nestemäiset käsittelykustannukset kadmiumin elektropnointiprosessissa ovat korkeat, ja sen hinta on noin 15-20-kertainen sinkin sähköpuhdistuksen hintaan. Joten sitä ei käytetä yleisellä teollisuudessa, vain tietyissä ympäristöissä. Kiinnittimet, joita käytetään öljyporausalustoihin ja HNA -lentokoneisiin.
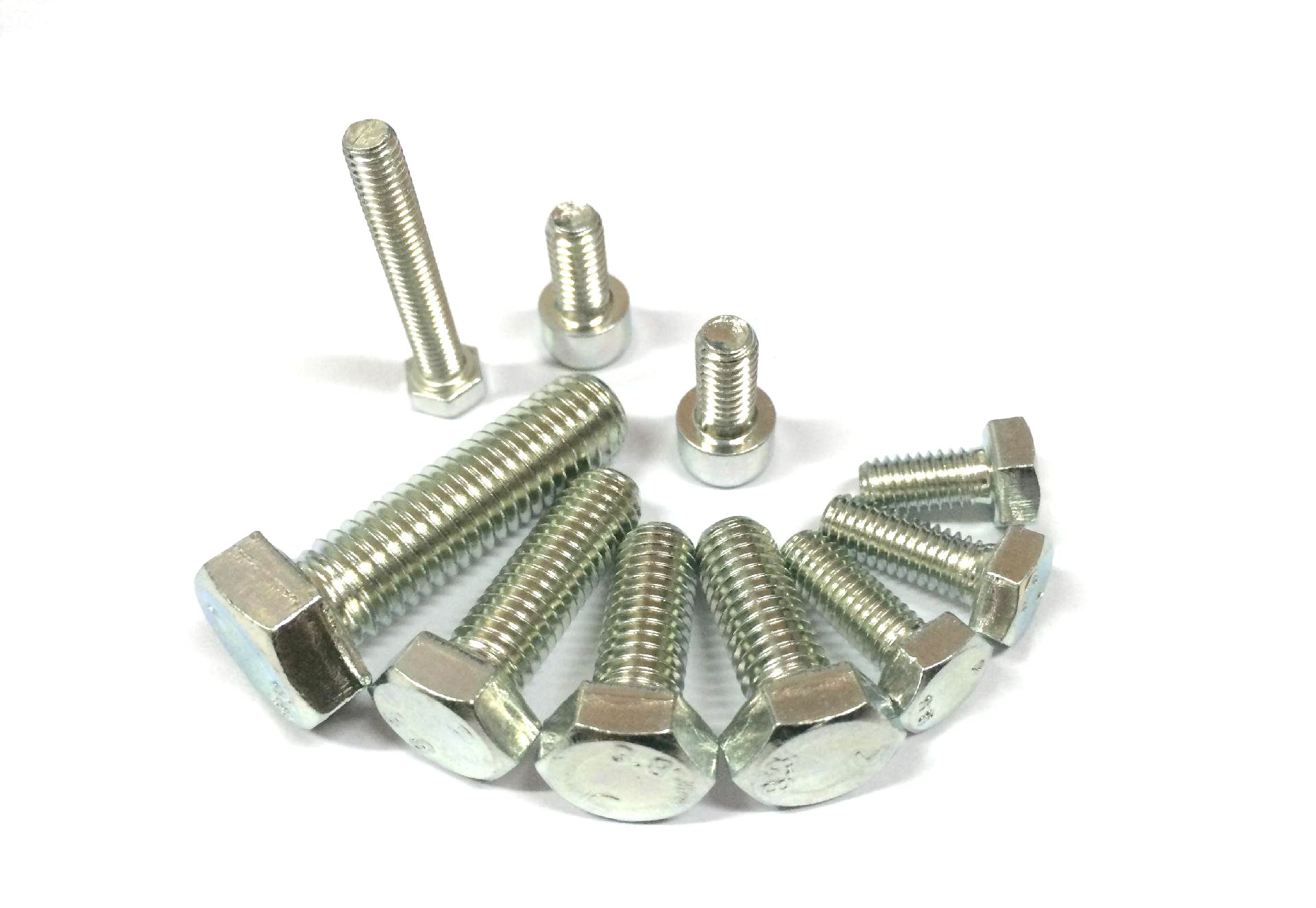
5. Kromipinnoitus
Kromipinnoite on erittäin vakaa ilmakehässä, ei ole helppo muuttaa väriä ja menettää kiiltoa, ja sillä on suuri kovuus ja hyvä kulumiskestävyys. Kromipinnoituksen käyttöä kiinnittimissä käytetään yleensä koristeellisiin tarkoituksiin. Sitä käytetään harvoin teollisuusalueilla, joilla on korkea korroosionkestävyysvaatimus, koska hyvät kromattujen kiinnittimet ovat yhtä kalliita kuin ruostumattomasta teräksestä. Vain kun ruostumattomasta teräksestä valmistettu lujuus ei ole riittävä, sen sijaan käytetään kromattuja pinnoitettuja kiinnittimiä.
Korroosion estämiseksi kupari ja nikkeli tulisi pinnoittaa ensin ennen kromipinnoitusta. Kromipinnoite kestää korkeita lämpötiloja 1200 astetta Fahrenheit (650 ℃). Mutta on olemassa myös vetyhallinnon ongelma, samanlainen kuin sähkögalvanisointi.
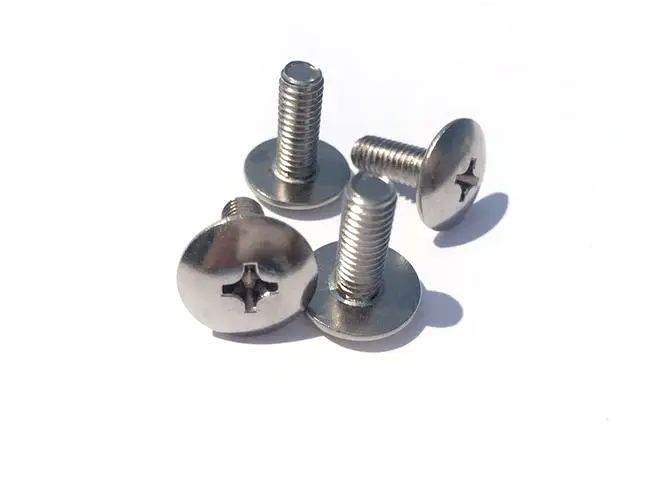
6. Nikkelipinnoitus
Käytetään pääasiassa alueilla, jotka vaativat sekä korroosion vastaista että hyvää johtavuutta. Esimerkiksi ajoneuvoparistojen lähtevät päätteet.
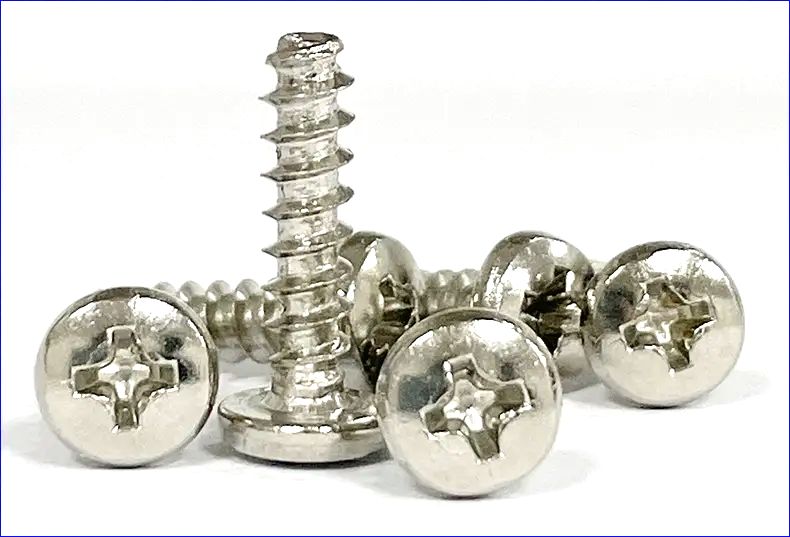
Klo 7. kuuma-dip galvanointi
Kuuma dip -galvanointi on sinkin lämpö diffuusiopäällyste, joka on lämmitetty nesteelle. Pinnoitteen paksuus on välillä 15 - 100 μm. Ja sitä ei ole helppo hallita, mutta sillä on hyvä korroosionkestävyys ja sitä käytetään usein tekniikassa. Kuuman dip -galvanisointiprosessin aikana pilaantumista on vakava, mukaan lukien sinkkijätteet ja sinkkihöyry.
Paksun pinnoitteen takia se on aiheuttanut vaikeuksia ruuvaamisessa kiinnittimissä sisä- ja ulkoisiin kierteisiin. Kuuma-dip-galvanisoivan prosessoinnin lämpötilan vuoksi sitä ei voida käyttää luokan 10,9 yläpuolella oleviin kiinnikkeisiin (340 ~ 500 ℃).
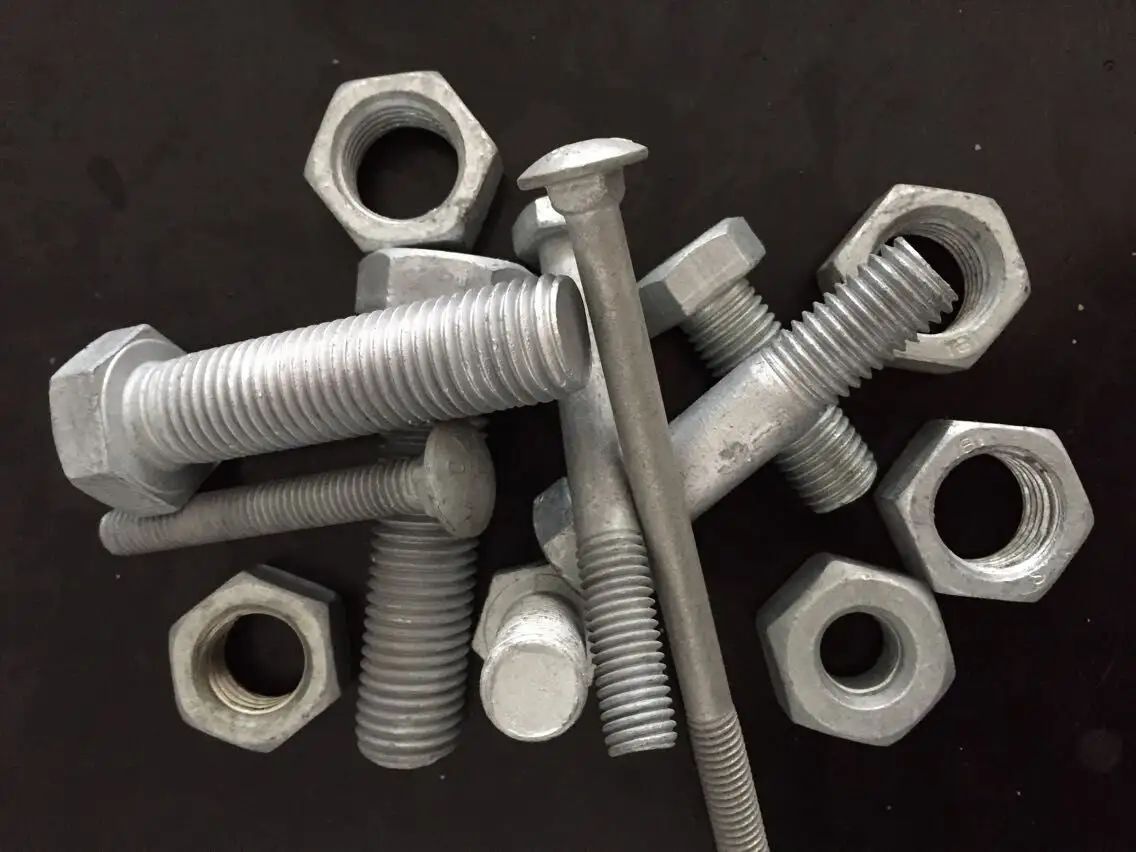
8. Sinkin tunkeutuminen
Sinkin tunkeutuminen on sinkkijauheen kiinteä metallurginen lämpödiffuusiopäällyste. Sen tasaisuus on hyvä, ja tasainen kerros voidaan saada sekä kierteisiin että sokeisiin reikiin. Pinnoituspaksuus on 10-110 μm. Ja virhettä voidaan hallita 10%: lla. Sen sidoslujuus ja korroosionestojen vastainen suorituskyky substraatin kanssa ovat parhaita sinkkipinnoitteissa (kuten elektrogalvantaatio, kuumin galvanointi ja dacromet). Sen prosessointiprosessi on pilaantumaton ja ympäristöystävällisin.
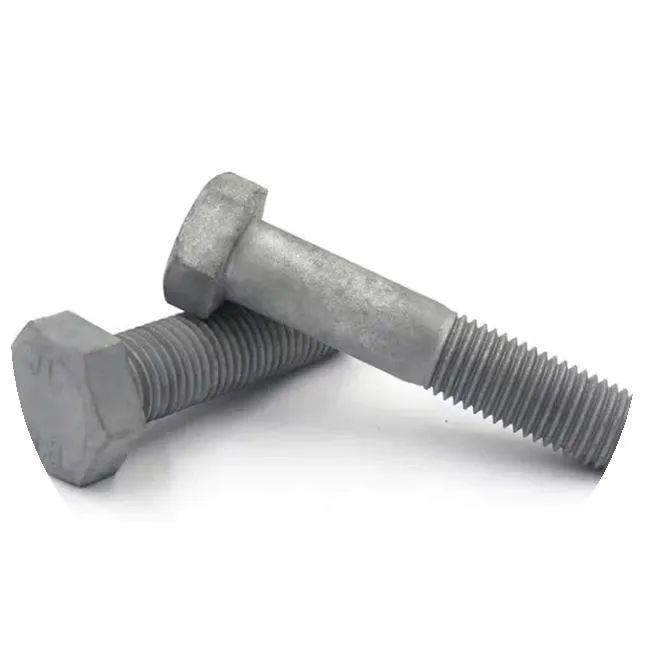
9. Dacromet
Vetyhallintakysymystä ei ole, ja vääntömomentin preload -johdonmukaisuuden suorituskyky on erittäin hyvä. Dakromet on tosiasiallisesti sopivin kromi- ja ympäristökysymyksiin, ja se on todella sopivin korkean lujuuden kiinnittimille, joilla on korkea korroosionestovaatimus.
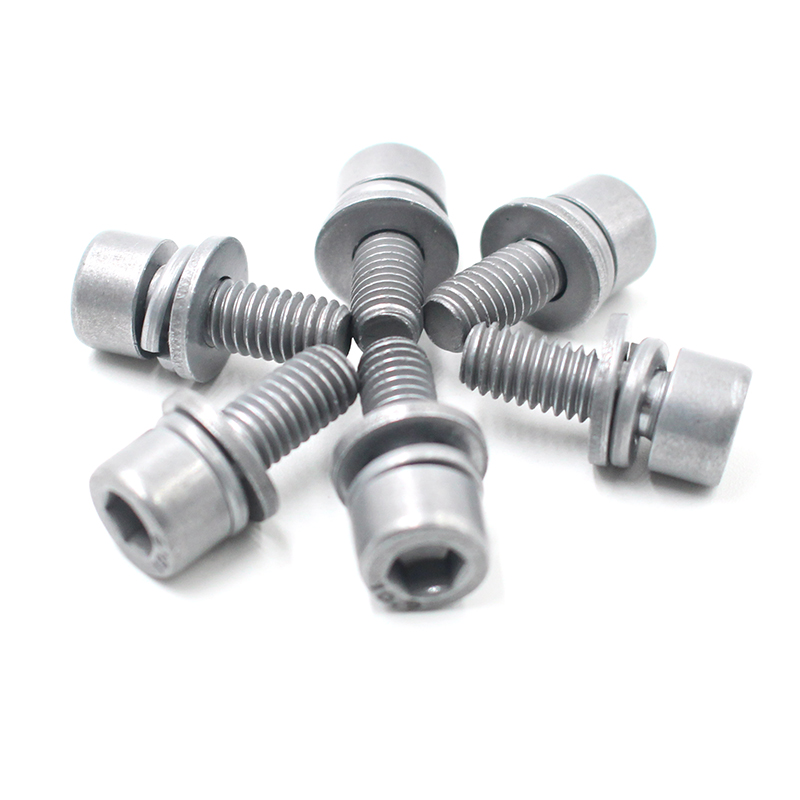
Viestin aika: toukokuu-19-2023